Refractory knowledge
- Physical properties of refractory materia
- How to Bake High Alumina Bricks
- Lightweight fire brick performance
- Introduction to the production process of
- Improve the service life of chrome corund
- How to improve the insulation performance
- The origin and development of refractory
- The production process of Refractory Bric
Hot Products
Application Effect of Energy Saving Material Aluminum Silicate Fiber
Aluminosilicate refractory fiber is a new type of fire-resistant insulation material. Statistics show that the use of aluminum silicate refractory fiber as resistance furnace refractory or insulation material can save energy consumption by more than 20%, and some up to 40%. Because the aluminum silicate refractory fiber has the characteristics of high temperature resistance, good chemical stability, and low thermal conductivity, the use of aluminum silicate refractory fiber as the lining of the resistance furnace in the non-ferrous metal casting workshop can shorten the heating time and reduce the wall temperature and energy consumption. . Aluminum silicate fiber has the following features.
(1) High-temperature resistant Ordinary aluminum silicate refractory fiber is an amorphous fiber made of refractory clay, bauxite or high-alumina raw material in the molten state using a special cooling method, the use temperature is generally below 1000 °C, and some Up to 1300°C. This is because the thermal conductivity and heat capacity of the aluminosilicate refractory fiber are close to the air. It consists of solid fibers and air and has a porosity of more than 90%. Because a large amount of low thermal conductivity air is filled in the pores, the continuous network structure of the solid molecules is destroyed, thereby having excellent heat-resistant and heat-retaining performance. (2) Chemical stability The chemical stability of the aluminosilicate refractory fiber depends mainly on its chemical composition and impurity content. The alkali content of this material is extremely low, it hardly reacts with hot and cold water, and it is very stable in an oxidizing atmosphere. However, in a strong reducing atmosphere, Fe2O3, TiO2 and other impurities in the fiber are easily reduced, affecting the service life.
3) Capacity and Thermal Conductivity With different production processes, there is a large difference in the capacity of aluminum silicate refractory fibers, generally in the range of 50~200kg/m3. The size of thermal conductivity is the main indicator to measure the performance of refractory insulation materials. The small thermal conductivity is one of the important reasons why aluminum silicate refractory fibres have better fire-resistance and thermal insulation performance than other similar materials. In addition, its thermal conductivity is the same as that of other fire-resistant insulation materials, and it is not constant. It is related to the bulk density and temperature.
The heat generated by the heat-generating resistance furnace of the aluminum silicate refractory fiber can be divided into two parts. The first part is used to heat or melt the metal. The second part is the heat storage of the lining material, the cooling of the furnace wall and the heat generated by opening the furnace door. loss.
To make reasonable use of energy, it is necessary to minimize the above-mentioned second part of the heat loss and increase the effective utilization of the heating element. The choice and conversion of the lining material has a significant effect on the heat storage loss and the total heat loss.
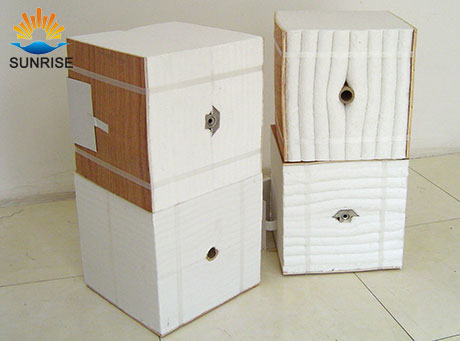