Refractory knowledge
- The origin and development of refractory
- The impact of Sino-US trade war on the re
- Physical properties of refractory materia
- Introduction to the production process of
- How to Bake High Alumina Bricks
- Improve the service life of chrome corund
- The production process of Refractory Bric
- Lightweight fire brick performance
Hot Products
Introduction to the production process of refractory castables
With the wide application of refractory castables, the production method of refractory castables has also received attention. In fact, materials such as refractory ramming materials and refractory spray coatings have the same production process as refractory castables.
In the production process of refractory castables, some raw materials do not need to be broken and crushed, and can be used directly. For example, alumina hollow spheres, ceramsite, expanded perlite, and industrial alumina. Select the main equipment according to factors such as production scale, raw material varieties and their characteristics:
1. Crushing - There are three types of jaw crushers. The specifications are expressed in the size of the inlet. The main ones are 250mm × 400mm, 600 mm × 400mm, etc. The production capacity is 5~20t/h, which is used for coarse crushing of large blocks. .
Crushing - refers to the medium crushing and fine crushing of the refractory raw material, which is also the preparation of the pellet material. The equipment used is a cone crusher, a roller crusher and a dry mill.
2. Screening - The pulverized material is divided into pellets of different particle sizes according to the particle size. The equipment used is a fixed diagonal screen and an electromagnetic vibrating screen. The former has a screening efficiency of about 70%, and the latter is generally more than 90%.
3. Fine grinding - refers to the production of refractory powder. The equipment used therein is a ball mill, a tube mill and a vibrating mill;
4. Pre-mixing - refers to the pre-mixing of all powders or certain powders such as admixtures, admixtures, binders and fine powders, so it is called pre-mixed powder. The equipment used is a double spiral conical mixer or the like.
5. Batching scale - generally used electronic type, accurate weighing; the mixer uses a forced mixer, the mixing material can be input into the filling machine and then sub-packaged, or can be directly packed into bags from the outlet of the mixer;
In addition, there are vertical hoists, belt conveyors and batching vehicles.
For the production of refractory castables, the preparation of refractory aggregates and powders, soft clay and other raw materials is basically the same as that of fired refractory bricks. The difference is that the refractory aggregates have large critical particle size and many grades, so screening is required. There are many equipments such as lifting, and there are many storage bins. At the same time, it is necessary to prepare a premixed powder, which is a special process. Premixed powders must be used in the production of high-grade refractory castables. Otherwise, a small amount of additives such as admixtures, ultrafine powders and fibers are difficult to mix, resulting in unstable performance and affecting construction and use.
After the preparation of various raw materials, they are separately loaded into the silo for use. The silo is divided into fixed and mobile. The indeterminate silos are overhead, and the various raw materials are lifted by the hoist to the belt conveyor at the bottom of the silo and then distributed to each silo. There are electronic scales and batching carts under the silo, and the ingredients are prepared according to the production mix ratio of the refractory castables. Then, the prepared material was put into a forced mixer and mixed for about 5 minutes. The mixed refractory castable mixture is put into the sub-assembly equipment from the discharge port of the mixer. The bottom of the equipment has an electronic scale. After weighing, the bag is packed or boxed. Finally, the sealing machine is used to seal the bag or use tape. Paper sealing mouth. Then transport the finished product to the warehouse and store it separately according to the grade and grade. The production line is three-dimensional operation, the plant is tall, the equipment is more, the degree of automation is higher, the quality of the material is more stable; the mobile silo is placed on the floor of the workshop, and the material is transported to the top of the silo by the hoist and belt conveyor, and is divided into It can be loaded into the silo and can also be loaded by crane. The bottom of the silo is equipped with a scale or electronic scale ingredients, equipped with a good material, loaded into the hopper of the mixer with a belt conveyor or a trolley, and then mixed, the remaining process is the same as before. The production line operates horizontally, covers a large area, has few equipments, and is flexible in operation, and can also ensure the quality of materials.
For finished products of refractory castables, the quality of heavy materials is generally 30~50kg per bag, and that of light materials is 20~30kg per bag, with an error of ±0.2kg.
In the production of refractory castables, when cement or liquid binder is used, it can be dispensed or shipped directly to the user, but the warranty period and dosage must be indicated; the refractory castables such as clay combination and low cement series are also classified as cement. Installed. If the cement expires, it is easy to replace. If used within the 3-month shelf life, it should also be mixed.
Chemical analysis and physical properties of refractory raw materials, cement binders and additives shall be carried out before the refractory castables are mixed; the refractory aggregate after pulverization and the refractory powder after fine grinding shall be subjected to chemical analysis and sieving. Inspection of points and fineness.
The production mix ratio of refractory castables shall be produced only after the raw materials and production processes have changed, and must be tested to meet the technical requirements; the production of new varieties of refractory castables shall be retested; When producing refractory castables, the particle grading shall be inspected. If it does not meet the technical requirements, it shall be adjusted in time; the finished products of each batch of refractory castables shall be tested according to technical requirements, and the quality assurance and construction technical requirements shall be issued. , sent to the user.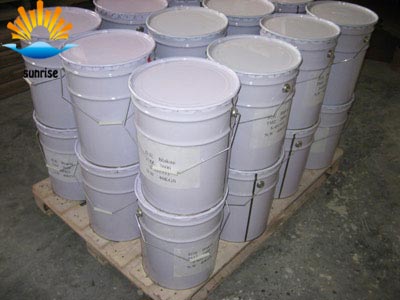
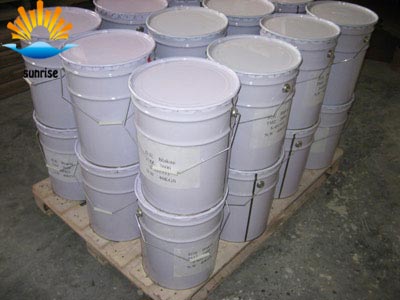