Refractory knowledge
- Application of Lightweight Clay Brick in
- The production process of Refractory Bric
- How to improve the insulation performance
- Physical properties of refractory materia
- Introduction to the production process of
- The impact of Sino-US trade war on the re
- How to Bake High Alumina Bricks
- Improve the service life of chrome corund
Hot Products
Difference between high aluminum refractory and clay refractory
As we all know, refractory performance is good or bad with the refractory aluminum content is very close, then we usually use high alumina refractories and clay refractory What is the difference, the following general knowledge to popularize refractory .
High alumina refractories and clay refractories compared to the outstanding advantages of refractoriness and load softening temperature is high, with the increase of Al2O3 content, slag resistance significantly improved. (1) Refractoriness. High refractory aluminum refractory range, typically 1770 ~ 2000 ℃, mainly affected by the content of Al2O3, with the increase in the content of Al2O3 increased. At the same time, the refractoriness is also affected by the content and type of impurities, which is related to the structure of the product phase. (2) load softening temperature. The deformation temperature of high alumina refractories begins to soften to more than 1400 ℃, and increases with the increase of Al2O3 content. (3) thermal conductivity. High alumina refractory products than clay products with high thermal conductivity. The reason is that the glass with low thermal conductivity in high aluminum products is less, while the amount of mullite and corundum crystals with better thermal conductivity is increased, which improves the thermal conductivity of the products. (4) Thermal shock resistance. High thermal shock resistance of aluminum refractory products between the clay products and silicon products. 850 ℃ water-cooled cycle only 3 to 5 times. This is mainly due to the thermal expansion of corundum mullite than high, and no crystal transition. (5) slag resistance. High aluminum refractory products can resist acidic slag erosion, but also can resist the role of alkaline slag. However, the ability of anti-alkaline slag less than the magnesia, but better than the clay material, and with the mullite and corundum content increases.
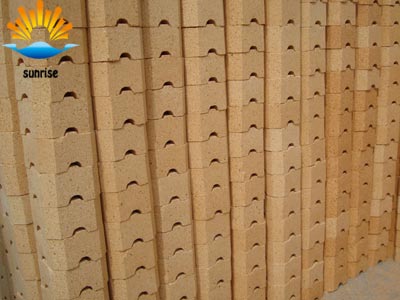
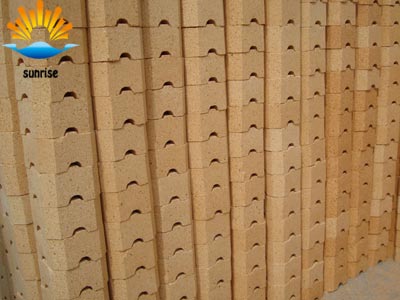