Refractory knowledge
- Application of Lightweight Clay Brick in
- How to Bake High Alumina Bricks
- Physical properties of refractory materia
- Improve the service life of chrome corund
- The impact of Sino-US trade war on the re
- Introduction to the production process of
- Lightweight fire brick performance
- The production process of Refractory Bric
Hot Products
Regenerative chamber of the working principle and role
The regenerator is a periodic heat exchanger, which belongs to the cyclical unstable temperature field. The heat transfer process is unsteady heat transfer. The working characteristics are similar to the countercurrent heat exchanger, so the regenerator is usually regarded as the counterflow heat exchanger To analyze the entire cycle of heat transfer, thus simplifying the problem.
In the process of heat transfer, the exhaust gas mainly conveys the heat to the surface of the lattice body by convection, and then transfers the heat to the lattice body through the heat conduction; while the heating air mainly convects the heat through the convection and radiation Air, because the air of O2, N2 is a symmetrical two atoms, not radiation or absorption, so the temperature is still high mainly convection heat; heating gas, the radiation can be strengthened. Commutation time has a greater impact on the heat exchange efficiency of the regenerator, the more appropriate time is analyzed as 20 ~ 25min. In addition, the density of bricks, the specific heat capacity, arrangement and gas flow channels also affect the heat exchange process is good or bad. The flow of gas in the regenerator, mainly the uniform distribution of the airflow on the cross section, is of great significance for improving the heat transfer and improving the thermal efficiency. The direction of gas flow should be consistent with the rules of gas vertical movement, that is, flue gas flows from top to bottom, air or gas flows from bottom to top. Compared with the vertical ascending path regenerator, the box regenerator improves the airflow distribution, increases the volume of the lattice, improves the thermal efficiency and reduces the heat dissipation area. The larger the cross-sectional area of regenerator, the more uneven the air flow distribution, especially at the corner, so the upper part of the box regenerator should have enough height.
Its working principle is: when the kiln high temperature exhaust gas from the top down through the small mouth and air, gas channel into the regenerator, the regenerator within the lattice heating, when the lattice temperature gradually increased, a certain savings Of the heat; after the fire, the combustion air and gas from the bottom up through the bottom of the regenerator flue into the regenerator, the regenerator within the lattice body with the accumulated heat to preheat the air and gas, then the lattice Temperature gradually decreased. The working process as shown below shows the regenerative work.
It can be seen that the work of the regenerative chamber is cyclical, one cycle is the heating period of the lattice body, the other is the cooling period of the lattice body, and so the cycle is repeated. Therefore, the role of regenerator is: the use of lattice bricks as a regenerator, the heat contained in the exhaust accumulated, after exchange of heat with the accumulated heat to the air and gas preheated to a certain temperature.
The general air can be preheated to 1000 ~ 1200 ℃; gas can be preheated to 800 ~ 1000 ℃; exhaust gas regenerator temperature of about 600 ℃. In order to meet the airflow distribution and meet the requirements of heat transfer area. It is necessary to increase the height of the regenerator and the rational arrangement of lattice body. The use of three-channel regenerator is an effective measure.
Since the temperature of flue gas, lattice and air in each commutation cycle changes with time, the temperature changes very fast in a very short time just after commutation, and then the speed of change gradually becomes slower. For single-channel regenerators. Due to commutation caused by the temperature fluctuations, and the use of multi-channel temperature field will be able to stabilize. Of course, due to the longer flue gas flow, air flow resistance increases, so the chimney need to be raised or smoke extractor to increase pumping force.
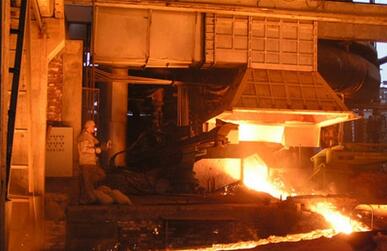
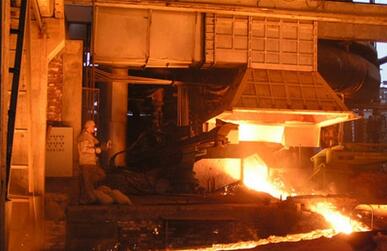