Refractory knowledge
- Introduction to the production process of
- Physical properties of refractory materia
- Application of Lightweight Clay Brick in
- The origin and development of refractory
- Lightweight fire brick performance
- The impact of Sino-US trade war on the re
- The production process of Refractory Bric
- How to Bake High Alumina Bricks
Hot Products
Corundum refractory mud
Refractory clay is a monolithic refractory material used to prepare a slurry of powdered refractory materials and binders. It is mainly used for masonry brick masonry joints and as a coating material. As a puzzle material or paint use, require the same material and refractory bricks.
As a joint refractory mud, the quality of its quality masonry have a considerable impact. Its main function is to adjust the size of refractory bricks and irregular shape to make the masonry neat and load balanced and can make the masonry form a tight and strong overall to resist the destruction of external forces to prevent gas and metal melting Liquid intrusion.
The preparation of corundum fire mud is mainly using 0.5 ~ 0.63 mm and finer sintered corundum clinker or fused corundum fused fused alumina with 5 ~ 7μm or less than 5μm industrial alumina binder, industrial alumina does not exceed 15 % ~ 20%, fused alumina corundum to reach 40% to 50%, the introduction of orthophosphoric acid (density 1.72 g / cm3) 10%.
The performance of corundum cement is required to match the performance of the masonry corundum brick and to withstand the same chemical and physical effects in the furnace as corundum bricks at high temperatures. In particular, the requirements of petrochemical enterprises for high-temperature furnace overall structural better, airtight, brickwork joints to be smaller (less than 1 mm), so require corundum mortar fineness, good adhesion, bonding Time should not be too short.
With refractory clay produced from sintered corundum clinker, masonry joints with a thickness of less than 1.5 mm can not be made without using sodium phosphate and other additives and without increasing moisture. They use 5 ~ 15μm 94.5% alumina, 5.5% ground sodium polyphosphate, 0.1% fermented alcohol waste, the fire clay in the case of normal consistency, the water 21% to 22%, to ensure masonry Brick seam thickness of 0.8 ~ 1.0 mm. However, this fire mud shrunk at 1300 ℃ up to 5%, but did not produce small cracks and cracks; 1500 ℃ after burning more dense than the use of sintered corundum clinker made of solid strong.
The porosity of refractory mud increases, and the shear bond strength tends to decrease.
In order to make the corundum refractory mud moisture uniformity, to maintain the poor water at the level of 2.5%, to remove some dust, the introduction of CaCl2 2.5%. This increases the moisture content of the mud to 24% to 27%, while the cohesive strength of the fire clay and the corundum refractory does not decrease. The shear bond strength at 1000 ° C is equal to 1.4 to 2.0 MPa and reaches 1500 ° C 10 MPa.
Phosphate bonded corundum refractory mud and paint, thermal shock resistance and slag resistance is better. Corundum paint is estimated to be better by high alumina brick), can withstand 1300 ℃ and cold water repeatedly exchanged 40 times, no cracking.
Most of China's preparation of corundum refractory mud fused corundum, sintered corundum as raw materials, and adding water-reducing agent, aids and so on.
DMT residue treatment furnace of a petrochemical company in Tianjin is made of corundum-mullite masonry. The refractory mud used is mainly fused alumina, sintered corundum, sintered mullite and clay. The particle size is less than 0.074 mm and 85% -90 %, With sulfonate organic matter 2% to 3% as a water-retaining agent, phosphate 1.5% as a water-reducing agent, and appropriate to join aids. Some people use high alumina and corundum and added phosphoric acid to make phosphoric acid corundum mud.
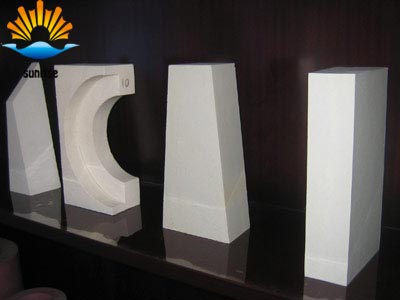
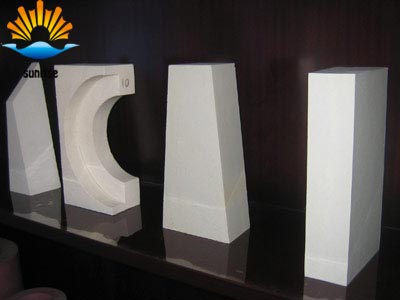