Refractory knowledge
- Lightweight fire brick performance
- How to improve the insulation performance
- The origin and development of refractory
- The impact of Sino-US trade war on the re
- The production process of Refractory Bric
- Application of Lightweight Clay Brick in
- Improve the service life of chrome corund
- Introduction to the production process of
Hot Products
Refractory materials production process of energy saving and environmental protection
Refractory production process is roughly as follows: raw material mining - raw materials calcined or fused - broken and crushed - screening - ingredients and mixing - forming - drying - firing - testing - finished products. The following orderly analysis of refractory material production process of energy saving and environmental protection how to do: Mining. Refractories industry is a resource-based industry, the initial raw material is mined from mines. China's refractory output of about 24 million tons to 30 million tons, about 1.5 tons to 2.5 tons of raw materials to produce 1 ton of refractory material, therefore, the annual exploitation of refractory raw materials about 50 million tons to 60 million tons. China's refractory raw materials mines digging indiscriminately digging serious phenomenon, waste of resources, pollute the environment. In order to protect the environment, it is necessary to rectify the mining order of refractory raw material mines, strengthen management and conduct mining according to the mining technical specifications. At the same time, the abandoned rock and soil should be backflushed to the stope, land leveling, greening or rebuilding farmland.
Most of refractory raw ore and other beneficial minerals coexist in the mining, it should be fully exploited, respectively, to be used. Especially in coal mining, bauxite or coal gangue and refractory clay should be mined at the top or bottom of the coal seam at the same time. This not only avoids the waste of resources but also reduces the emission of waste. In addition, we should strengthen the use of low-grade ore research, to minimize waste emissions. Magnesite, bauxite mineral processing and purification is imperative. Another way to reduce mine production is to recycle spent residual refractory materials. According to relevant information, China's spent refractory after use about 4.5 million tons to 5.25 million tons per year, if this can be used after the recovery of refractory materials as refractory raw materials, not only to reduce the mining volume, and reduce waste emission.
Refractory raw materials calcined (or fused). Natural refractory raw materials mined from mines generally can not directly produce refractory materials, most of which require high temperature calcining (or electrofusion) of mature materials. This consumes a lot of energy on the one hand, on the other hand emits large amounts of flue gas and other harmful gases pollute the environment. So far, most of the flue gas produced by calcining refractory raw materials in our country has been discharged into the atmosphere and must be taken seriously. Fire-resistant raw materials calcination or electrofusion, emissions of pollutants must be controlled.
Calcination of refractory raw material equipment selection, we must pay attention. At present, with continuous production of mechanized shaft kiln, less investment, quick, high utilization factor, high production efficiency, low heat consumption, gas, fuel oil can also be used coke, coal and other solid fuels, and the temperature can be controlled , But also in the shaft kiln exhaust gas recovery installation, energy saving, environmental protection. Whether it is high-purity magnesia, plate-shaped corundum and other high-grade refractory raw materials, or general refractory clay, bauxite, can be used shaft calcined.
The best way to save energy and reduce emissions is to fire-resistant raw materials without calcination or electrofusion, with raw materials directly to produce refractory materials. The purpose of calcination of refractory raw materials is to make it stable in volume and to avoid the waste generated by the volume effect during the calcination of the product. In fact, there are many refractory raw materials in the heating process, the volume did not change much, such as wax stone, silica, olivine, andalusite, sillimanite, blue spar, zircon, etc., can use raw materials to produce refractory bricks and not Shape refractory materials, and have the actual production experience.
Refractory raw materials crushing, crushing, screening, ingredients and mixing. Whether stereotypes or amorphous refractory material, require raw materials reasonable particle size ratio. However, refractory raw materials are generally difficult to meet the grain size requirements, must be crushed, crushed, sieved in order to carry out the ingredients, mixed in this process inevitably produce dust, poor seal floating in the atmosphere, polluting the environment, endangering the human body health. Environmental protection departments must step up investigation of refractories, formulate strict standards for dust control, and eliminate backward and underqualified enterprises.
Products dry, firing. Drying temperature of the product is generally not high, most companies use products to burn the waste heat to dry, very few companies have a separate drying equipment. The higher the firing temperature of the product, the greater the energy consumption. In ensuring the use of the premise, lower firing temperature can save energy. There are many ways to reduce the firing temperature of products, such as adding superfine powder or nano powder, adding aiding agent, using special binding agent and the like.
If the refractory products do not burn, it is energy-saving. For example, high alumina brick firing temperature above 150 degrees Celsius, and phosphate combination of high alumina brick firing only about 50 degrees Celsius, the intensity is higher than the high temperature firing of high alumina bricks.
Refractory materials should be the direction of development of products as much as possible to burn bricks, amorphous refractory and non-burning brick to make use of recycled refractory materials as raw materials, of course, some raw materials can also be used, such as blue spar, Andalusite, pyrophyllite, olivine and the like. China's refractory industry should strengthen mergers and acquisitions, eliminate backward production capacity, improve overall strength, so as to be more capable of developing environment-friendly new products and strengthen environmental protection.
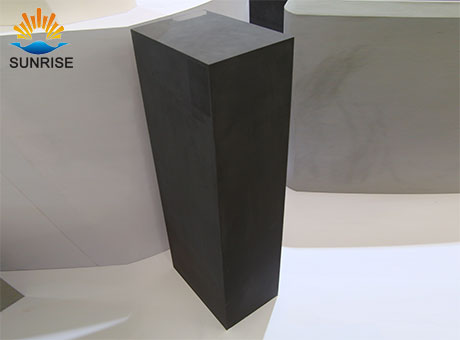
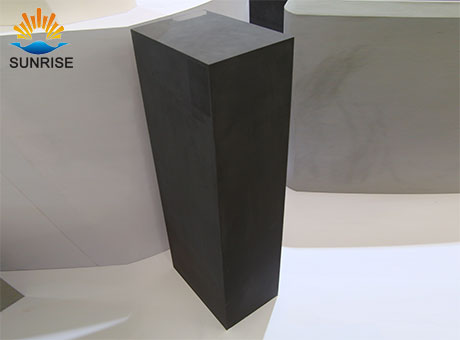