Refractory knowledge
- Introduction to the production process of
- The origin and development of refractory
- Physical properties of refractory materia
- Application of Lightweight Clay Brick in
- How to Bake High Alumina Bricks
- Improve the service life of chrome corund
- How to improve the insulation performance
- The production process of Refractory Bric
Hot Products
Hot stove light insulation brick
The purpose is to meet the need for high air temperature and longevity of the hot blast stove (this is very important). Understand these types of lightweight insulation bricks and carefully select insulation materials.
(1) Lightweight silica brick
Lightweight silica bricks are a new type of special material used in hot air furnace walls in the steel industry. Hot blast stoves are often used for high hot air passages, which are the same as blast furnaces. The temperature ranges from 1000 to 1300 °C depending on the shape and location of the hot blast stove. Its load deformation temperature reached 1620~1640°C. It has been proved by many cases that lightweight silica bricks can be used in kiln furnaces operating at a temperature of 1550-1600°C for a long period of time; they can be directly built on hot surfaces that are in contact with hot gases, and can also be used in large-span furnace tops.
(2) Diatomaceous earth insulation brick
Diatomite insulation brick is a lightweight heat preservation material made of diatomaceous earth as raw material. It has good heat insulation and insulation properties and can be used as a heat insulation layer on the back of clay brick. Product performance is stable and energy efficiency is significant. Its thermal conductivity and expansion coefficient are small, which can ensure the stability of high temperature equipment work. The hot working works have strong anti-leakage performance and are not easily bonded by the melt, and even resist local mechanical vibration in the kiln without cracking.
(3) Lightweight clay brick
Lightweight clay bricks are air-hole lightweight insulation materials, which are built on the back of clay bricks or lightweight high-alumina bricks and can be used as insulation. It can be used in areas where there is no strong high-temperature melt erosion and erosion. Some surfaces that are in direct contact with the flame are coated with a fire-resistant coating to reduce erosion by slag and furnace gas dust and reduce damage.
4) Lightweight high-alumina brick
Lightweight high-alumina bricks are good heat-insulating materials that can be used to masonry the back of high-alumina firebricks or lightweight silica bricks. It is mainly used for masonry kiln inner lining or thermal insulation layer and parts without strong high-temperature Rongrong material erosion and erosion. When in direct contact with the flame, the surface contact temperature is up to 1350°C. Features of lightweight high-alumina bricks: light weight; small shrinkage; impermeability; good shock resistance;refractoriness up to 700°C.
Summary: The selection of lightweight insulation bricks for hot blast stoves can be based on the type of refractory bricks laid on the working floor. In other words, when the working layer is built with silica bricks, the back of the silica bricks should be built with light silicon bricks; when the working layer is built with high-alumina firebricks, the back of the firebricks should be built with lightweight high-alumina bricks. . When the working layer is built with clay bricks, light clay bricks or diatomaceous earth insulation bricks should be built on the back of the clay bricks. Of course, in order to achieve a better work efficiency, a longer working life of the hot blast stove, and technical discussion and exchange with the thermal brick manufacturer before selecting the materials as far as possible, the purpose selected for use must be met. More insights can be explored together!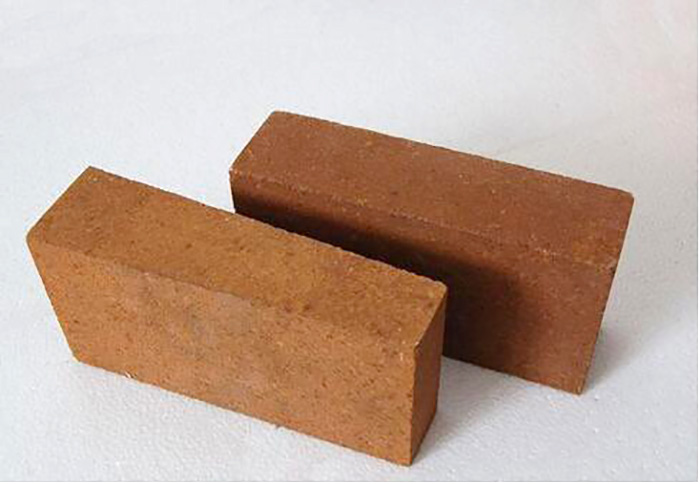
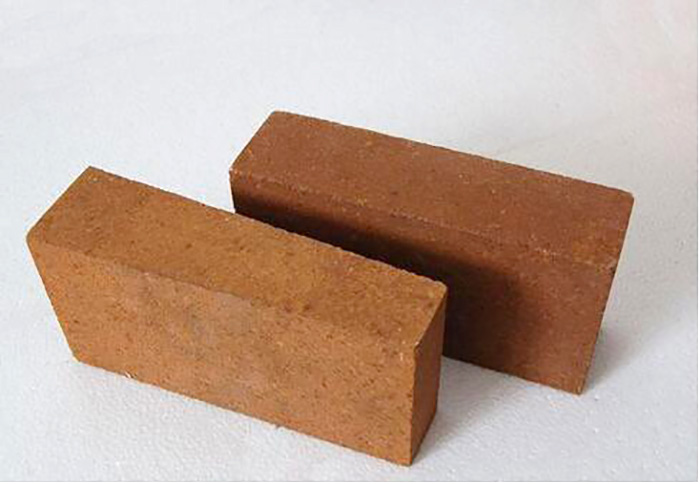